Why Capacitive Proximity Sensors Are Pushing Ahead on Packaging Lines
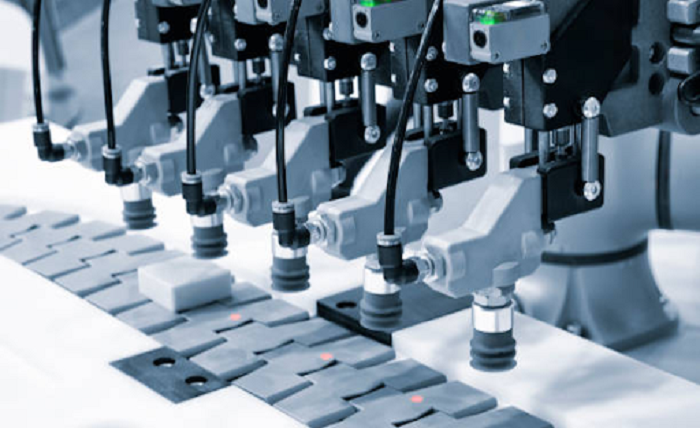
In the fast-moving world of factory automation, packaging lines keep getting trickier. Operators need sensors that are quick, clever, and able to work with many different materials. The capacitive proximity sensor now sits at the front of that technology pack because it does what older sensors struggle to do.
This post explains why these sensors are winning over packaging engineers and lists key points buyers should check before ordering from a reliable industrial parts dealer.
What Sets Capacitive Proximity Sensors Apart?
Capacitive sensors watch for tiny changes in electric capacitance whenever something gets close-nd it does not matter if that something is solid, liquid, or powder. Unlike inductive units that react only to metal, capacitive units see plastic, glass, cardboard, and even thin film of water through a bottle wall.
Because they work without touching anything, they suit delicate lines that cannot afford scratches or dust. Built-in filtering lets the sensor shrug off high humidity, light spray, or a fine layer of dust, giving engineers the flexibility they need on busy floors.
As a go-to supplier of industrial automation parts, we now notice many vendors widening their capacitive sensor ranges so they can tackle every packaging job, whether that job is food processing or filling pharmacy bottles.
Why Packaging Lines Need Capacitive Sensors
Packaging lines do a lot-handing materials, filling them, sealing, labeling, and double-checking quality. Regular mechanical switches or photo eyes often miss clear film, powder-filled sacks, or thin plastic trays because those targets barely register with standard detection.
That’s exactly why capacitive sensors stand out. Their advantages include:
- Non-contact detection:** They spot an object without touching it, guarding product quality.
- Material flexibility: They see liquids, solids, and even empty containers on a belt.
- Adjustable sensitivity: Engineers set the range to match the size and thickness of the target.
- Space-saving design: Slim housings fit where the room is tight and keep machines neat.
In vertical form-fill-seal (VFFS) lines, these sensors confirm film is in place before bags are shaped. On bottle-filling conveyors, they track liquid height through opaque or tinted walls.
When buyers or designers set out to choose the right sensor, they usually turn to a reliable automation parts distributor. That way, they can be sure each sensor matches the tough tasks of their unique packaging line.
Where Capacitive Sensors Shine in Packaging
These non-contact sensors now fit nearly every part of modern packaging machines. Here are the places you will see them most often:
- Level Checks at Filling Stations
In fill heads and tanks, capacitive sensors tell whether liquid or powder is there-even through thick walls. Because they never touch the product, cleanliness rules in food and medicine are much easier to follow.
- Label and Film Detection
Clear labels or shiny wrap can trick ordinary light beams, but capacitive units feel almost anything resting nearby. That means operators can keep the line moving without constant false stops or missed spots.
- Carton and Tray Presence Verification
Before a package is filled or sealed, these sensors confirm that each box or tray has arrived. Missing parts are caught early, saving material, time, and headaches further down the line.
- Object Counting and Sorting
On high-speed production belts, capacitive sensors quietly count even oddly shaped or plastic goods long before they reach packaging or pallet stations.
- Quality Control and Inspection
Same sensors spot missed fills or absent inserts, helping keep quality high on fast lines.
By working with a trusted industrial automation parts supplier, you secure the right tech and expert backing with every build.
Advantages Over Other Sensor Technologies
Inductive, ultrasonic, and photoelectric sensors all earn their keep, yet capacitive units offer distinct perks that shine in packaging work:
- Material-Agnostic: Sees almost anything, even low-dielectric plastics.
- Through-Barrier Sensing: Reads objects through jars, trays, or bags.
- Compact and Durable: Often IP-rated and shrugging off cleaning agents.
- Flexible Mounting: Fits snugly into the tightest frame or custom fixture.
Because they never touch what they sense, these sensors cut mechanical wear and power drain, guarding your line’s health over the long haul.
As packaging machines get smaller yet smarter, more plants turn to capacitive sensors for reliable, touch-free detection. Pair these sensors with a reliable industrial parts distributor that walks you through installation and fine-tuning, and you gain a fast, fuss-free upgrade.
Tips for Sourcing the Right Capacitive Proximity Sensor
Picking a capacitive sensor is about more than a single datasheet. Keep these points in mind:
- Sensitivity control: Choose models that let you tweak settings easily, either via knobs or a clear digital screen.
- Form factor: Decide between flush or non-flush mounting based on available room and mounting surface.
- IP rating: Check that the sensor shrugs off water, dust, and cleaning sprays.
- Output type: Match the sensor signal (PNP, NPN, relay) to your control circuit or PLC.
- Heat range: Pick a unit rated for the temp swings common in packaging areas.
Above all, lean on a reliable industrial parts distributor that offers technical advice, custom tweaks, and solid support after the sale so your new sensor performs to its fullest in the real world.
Conclusion: Smarter Packaging Is Here to Stay
Packaging lines are getting faster, greener, and a lot smarter, so the tools on those lines have to keep up. Enter capacitive proximity sensors. These little workhorses can spot almost any material, shrug off dust and moisture, and wear out far more slowly than other sensors.
If you’re upgrading an existing line or building a new one, make these sensors a key part of your plan. And to avoid headaches later, partner with a reliable industrial parts dealer who will back you with stock, advice, and service.
From food and medicine to picks and packs, capacitive sensing is becoming the new backbone of packaging. Are you ready to plug in?