VMCCAM: A Guide to VMC and CAM Technology
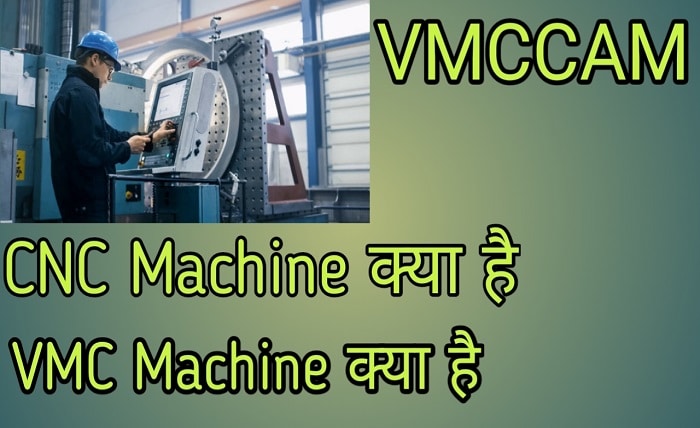
VMC and CAM are two terms that are often used in the fields of engineering, manufacturing, and design. VMC stands for vertical machining center, which is a type of CNC (computer numerical control) machine that can perform various operations on a workpiece, such as drilling, milling, cutting, etc. CAM stands for computer-aided manufacturing, which is software that can create and control the instructions for a CNC machine, such as the VMC.
We will explain what VMC and CAM are, how they work, what their advantages and disadvantages are, and how they are used in different industries and applications. We will also answer some frequently asked questions about VMC and CAM technology.
What is VMC?
A VMC is a type of CNC machine that has a spindle that can move vertically along the z-axis and a table that can move horizontally along the x and y axes. The spindle can hold various tools, such as drills, mills, cutters, etc., that can rotate at high speeds and perform different operations on the workpiece. The table can hold the workpiece securely and move it according to the instructions from the CAM software.
VMC machines can perform various operations, such as:
- Drilling: Making holes in the workpiece using a drill bit.
- Milling: Removing material from the workpiece using a rotating cutter.
- Cutting: Separating or shaping the workpiece using a blade or a saw.
- Tapping: Creating threads in the workpiece using a tap.
- Boring: Enlarging or finishing holes in the workpiece using a boring tool.
VMC machines can also perform other operations, such as engraving, carving, contouring, etc., depending on the type and shape of the tool and the workpiece.
What is CAM?
CAM is software that can create and control the instructions for a CNC machine, such as the VMC. CAM software can take a CAD (computer-aided design) file, which is a digital representation of the desired shape and dimensions of the workpiece, and convert it into a G-code, which is a set of commands that tell the CNC machine how to move and operate the tools and the table.
CAM software can perform various functions, such as:
- Toolpath generation: Creating the optimal path for the tool to follow on the workpiece based on the CAD file and the parameters of the machine and the tool.
- Simulation: Visualizing the toolpath and the resulting workpiece and checking for any errors or collisions before sending the G-code to the machine.
- Optimization: Improving the efficiency and quality of the machining process by adjusting the speed, feed, depth, etc. of the tool and the table.
- Post-processing: Converting the G-code into a specific format that is compatible with the CNC machine.
CAM software can also perform other functions, such as nesting, which is arranging multiple workpieces on the same table to minimize waste and maximize productivity, and verification, which is comparing the actual workpiece with the CAD file and measuring the accuracy and precision of the machining process.
What are the Advantages and Disadvantages of VMC and CAM?
VMC and CAM have many advantages and disadvantages, depending on the type and complexity of the workpiece, the cost and availability of the machine and the software, and the skill and experience of the operator. Some of the advantages and disadvantages are:
- Advantages:
- VMC and CAM can produce high-quality and precise workpieces with complex shapes and features that are difficult or impossible to make by hand or by conventional machines.
- VMC and CAM can reduce the time and labor required for the machining process by automating and optimizing the operations and eliminating the need for manual adjustments and measurements.
- VMC and CAM can increase the productivity and profitability of the machining process by enabling the production of more workpieces in less time and with less waste and errors.
- VMC and CAM can enhance the creativity and innovation of the machining process by allowing the creation of new and customized designs and products that meet the specific needs and preferences of customers.
- Disadvantages:
- VMC and CAM can be expensive and difficult to acquire and maintain, as they require a high initial investment, regular maintenance, and skilled operators and programmers.
- VMC and CAM can be limited and inflexible, as they depend on the availability and compatibility of the machine, the software, the tool, and the workpiece, and may not be able to handle all types and sizes of workpieces and operations.
- VMC and CAM can be risky and hazardous, as they involve high-speed and high-power tools and machines that can cause injuries or damages if not operated or controlled properly.
How are VMC and CAM Used in Different Industries and Applications?
VMC and CAM are widely used in various industries and applications, such as:
- Aerospace: VMC and CAM are used to produce parts and components for aircraft, rockets, satellites, etc., such as wings, fuselages, engines, etc., that require high precision and quality and can withstand extreme conditions and forces.
- Automotive: VMC and CAM are used to produce parts and components for vehicles, such as cars, trucks, motorcycles, etc., such as frames, bodies, engines, transmissions, etc., that require high performance and durability and can meet safety and environmental standards.
- Medical: VMC and CAM are used to produce parts and components for medical devices and equipment, such as implants, prosthetics, surgical instruments, etc., that require high accuracy and hygiene and can match the anatomy and physiology of the human body.
- Manufacturing: VMC and CAM are used to produce parts and components for various products and machines, such as appliances, furniture, tools, etc., that require high functionality and aesthetics and can satisfy the demand and expectations of the customers.
Conclusion
VMC and CAM are two terms that are related to CNC technology, which is a technology that uses computers to control and operate machines that can perform various operations on a workpiece. A VMC is a type of CNC machine that has a spindle that can move vertically and a table that can move horizontally and can hold various tools that can rotate and perform different operations on the workpiece. CAM is software that can create and control the instructions for a CNC machine and can take a CAD file and convert it into a G-code, which is a set of commands that tell the CNC machine how to move and operate the tools and the table.