Understanding the Differences Between 1045 and 1060 Carbon Steel
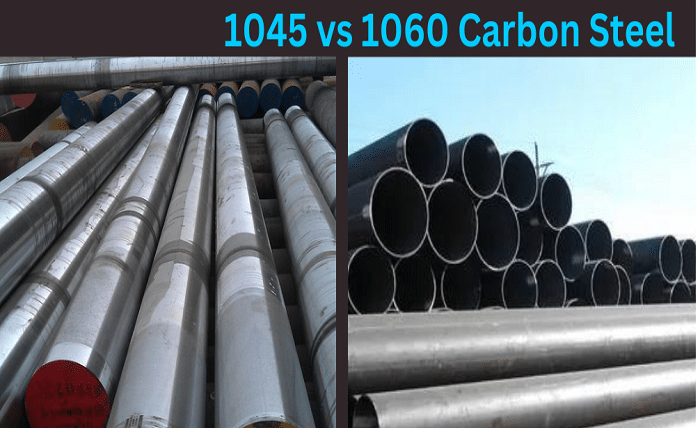
What Is 1045 Steel and How Is It Used?
1045 steel is a medium-carbon steel with a nominal carbon content of 0.45%. It is known for its good balance of strength, toughness, and wear resistance. 1045 steel possesses a tensile strength of approximately 570 MPa (or 82,700 psi) in its annealed condition, making it suitable for applications that require more strength and hardness than low-carbon steels. This type of steel can be heat-treated, quenched, and tempered to further enhance its mechanical properties, resulting in improved performance in demanding environments.
View Goldsupplier for More Details
1045 steel is widely utilized in various industrial applications due to its versatile properties. Common uses include the manufacture of axles, bolts, gears, and other machine components that require a robust and reliable material. Additionally, 1045 steel is often employed in the automotive and agricultural sectors for parts that need moderate wear resistance and toughness. The machinability of 1045 steel also makes it a preferred choice for producing precision components through processes such as CNC machining and forging.
If you are looking for more information about 1045 vs 1060 carbon steel go here right away
Characteristics of 1045 Carbon Steel
1045 carbon steel exhibits several important characteristics that make it a valuable material for various applications. Key properties of 1045 steel include:
- Medium Carbon Content: With a carbon content of 0.45%, this steel offers a good balance between strength and ductility.
- Tensile Strength: The tensile strength of 1045 steel is approximately 570 MPa (82,700 psi) in its annealed state.
- Hardness: This material can achieve additional hardness through heat treatment, such as quenching and tempering.
- Machinability: 1045 steel is known for its good machinability, making it suitable for processes like CNC machining and forging.
- Wear Resistance: It provides moderate wear resistance, which is desirable in applications with sliding or rotational movement.
Common Applications of 1045 Carbon Steel
Due to its versatile properties, 1045 carbon steel is used in a broad range of industrial applications, including:
- Axles
- Bolts
- Gears
- Machine components
- Automotive parts
- Agricultural equipment
Advantages of Using 1045 Steel
The advantages of using 1045 steel are numerous and contribute to its widespread use:
- High Strength and Hardness: Suitable for applications requiring enhanced mechanical properties.
- Good Machinability: Facilitates the manufacturing of precision components.
- Versatile Applications: Applicable in various sectors including automotive, agricultural, and machinery.
- Reliability: Offers reliable performance in moderately demanding environments.
- Heat Treatability: Can be quenched and tempered to further enhance its properties.
How Does 1060 Carbon Steel Compare to 1045?
Mechanical Properties of 1060 Carbon Steel
1060 carbon steel is recognized for its high carbon content, approximately 0.60%, which results in substantial tensile strength and improved hardness. This type of steel typically has a tensile strength of around 620 MPa (89,900 psi) in its fully annealed state. Its high carbon content makes it capable of achieving significant hardness through heat treatment processes such as quenching and tempering. Machinability of 1060 steel is moderate, and it is suitably forged, albeit with more difficulty compared to lower carbon steels. Wear resistance also benefits from the elevated hardness, making it ideal for high-impact applications.
Uses of 1060 Steel in Swords and Tools
Due to its unique mechanical properties, 1060 carbon steel is prominently utilized in the crafting of swords and various high-performance tools. In the realm of sword making, 1060 steel offers a perfect balance between hardness and flexibility, producing blades that are both strong and resilient to fractures. The ability to temper 1060 steel enhances its sharp edge retention, which is crucial for cutting tools and heavy-duty machetes. Blacksmiths and cutlery manufacturers often prefer 1060 steel for its capability to produce reliable and durable blades.
Benefits of Opting for 1060 Steel
Opting for 1060 carbon steel presents several advantages, particularly in applications that demand enhanced mechanical properties and durability:
- Superior Hardness: High carbon content allows the steel to reach a significant level of hardness, which is highly beneficial for cutting instruments.
- Edge Retention: Maintains sharpness over prolonged use, making it ideal for blades and tools that undergo substantial wear and tear.
- Strength: Provides excellent tensile strength, offering robustness in demanding applications.
- Heat Treatability: Can be effectively heat treated to adjust its hardness and ductility, tailored to specific application requirements.
- Versatility: Suitable for different applications, ranging from agricultural tools to high-quality swords, due to its robust mechanical properties.
What Are the Mechanical Properties of 1045 vs 1060?
Differences in Hardness and Durability
Understanding the differences in hardness and durability between 1045 and 1060 carbon steel is crucial for selecting the right material for specific applications. 1045 steel, with a lower carbon content of 0.45%, possesses moderate hardness and strength, making it suitable for components where high toughness and impact resistance are required. Conversely, 1060 steel contains 0.60% carbon, resulting in a higher hardness level, which is beneficial for applications necessitating a sharp and durable edge. The increased carbon content in 1060 steel contributes to its superior wear resistance and edge retention, making it a preferred choice for cutting tools and blades.
Effect of Carbon Content on Performance
The carbon content significantly influences the performance characteristics of steel. Higher carbon content enhances hardness and tensile strength but can also reduce ductility and impact resistance. In 1045 steel, the lower carbon percentage affords greater malleability and a lower risk of brittleness, making it ideal for parts that experience frequent stress and need to absorb higher impacts. On the other hand, the higher carbon content in 1060 steel delivers better edge sharpness and durability, crucial for tools and applications where maintaining a sharp edge is essential. However, this comes at the cost of reduced toughness and increased brittleness.
Comparison of Brittleness
Brittleness is a key factor to consider when comparing 1045 and 1060 carbon steel. 1045 steel, with its lower carbon content, exhibits greater ductility and impact toughness, meaning it can withstand sudden shocks and stress without fracturing. This makes it suitable for applications that demand a balance between strength and flexibility, such as in automotive and machinery parts. In contrast, the higher carbon content in 1060 steel, while providing enhanced hardness, also makes it more prone to brittleness. This characteristic necessitates careful heat treatment processes to ensure the material does not fracture under high stress or impact conditions, particularly in applications involving heavy-duty tools and weapons.
How to Tell the Difference Between 1045 and 1060 Steels?
Visual and Physical Inspection Methods
When differentiating between 1045 and 1060 carbon steel, initial visual and physical inspection methods can be an effective first step. These steels often exhibit slight variations in surface appearance, with 1060 steel typically appearing darker due to higher carbon content. Physical tests, such as hardness testing, can also distinguish between the two. 1060 steel, being harder, will exhibit higher resistance to indentation compared to 1045 steel. Another method is the spark test, where 1060 steel tends to produce more frequent and shorter sparks as a result of its higher carbon content.
Chemical Analysis Techniques
For precise differentiation between 1045 and 1060 steels, chemical analysis techniques are indispensable. Spectroscopy methods, such as X-ray fluorescence (XRF) and optical emission spectroscopy (OES), are commonly employed to determine the exact carbon content in the steel samples. XRF analysis involves bombarding the sample with X-rays and measuring the secondary X-rays emitted by the elements within the steel, while OES excites the sample with an electrical discharge and analyzes the resultant light spectrum. These techniques provide accurate, quantitative measurements of the carbon and other alloying elements, thereby confirming the specific type of steel.
Does Heat Treatment Affect 1045 and 1060 Steels Differently?
Role of Quenching in Steel Performance
Quenching is a crucial process in heat treatment that significantly impacts the mechanical properties of steel, including 1045 and 1060 carbon steels. This process involves heating the steel to a specific temperature and then rapidly cooling it by immersion in a quenching medium such as water, oil, or brine. The primary purpose of quenching is to enhance hardness and strength by achieving a martensitic transformation. For 1060 steel, quenching results in higher hardness and wear resistance due to its higher carbon content, whereas 1045 steel, though it also benefits from quenching, shows comparatively lower hardness and strength.
Impact of Heat Treating on Durability
The heat treatment process, which includes annealing, normalizing, quenching, and tempering, profoundly influences the durability of 1045 and 1060 steels. Annealing, which involves slow cooling, enhances ductility and reduces internal stresses, making the steel easier to work with. Normalizing, which involves air cooling, refines the grain structure for improved toughness. Quenching, as previously discussed, increases hardness but can introduce brittleness if not followed by tempering. Overall, 1060 steel responds more significantly to heat treatment due to its higher carbon content, resulting in higher hardness and strength but also requiring careful balancing to avoid excessive brittleness.
Tempering Processes for Each Steel Type
Tempering is the subsequent stage following quenching, intended to reduce brittleness while retaining the enhanced mechanical properties achieved during quenching. For 1045 steel, tempering at a lower temperature range (approximately 300-400°C) is often sufficient to achieve a desirable balance between toughness and hardness. In contrast, 1060 steel may require a higher tempering temperature range (400-600°C) to adequately temper the higher hardness attained during quenching. The exact tempering parameters, including temperature and time, must be meticulously controlled to suit the specific requirements of the application, ensuring optimal performance characteristics for each steel type.
Are 1045 Swords Different from 1060 Swords?
Blade Performance Comparison
When comparing the blade performance of 1045 and 1060 swords, several factors come into play, including edge retention, flexibility, and overall durability. 1045 steel, with its lower carbon content, offers greater flexibility, which makes it less prone to breaking under stress but can result in lesser edge retention compared to 1060 steel. On the other hand, 1060 steel provides a harder blade with superior edge retention and cutting performance, though it may be more brittle if not properly tempered. Therefore, 1045 swords are generally more forgiving and better suited for beginners, while 1060 swords are favored by experienced practitioners seeking higher performance and reliability.
Maintenance and Rust Prevention
Proper maintenance and rust prevention are crucial for preserving the functionality and appearance of both 1045 and 1060 steel swords. Regular cleaning and oiling are necessary to prevent rust, as both types of steel are susceptible to corrosion. After each use, the blade should be wiped clean of any moisture or residue, and a thin layer of oil should be applied to create a protective barrier against oxidation. Additionally, storing the sword in a dry environment, preferably in a scabbard or sheath with proper ventilation, will further mitigate the risk of rust and prolong the blade’s lifespan.
Choosing the Best Sword for Your Needs
Selecting the right sword depends largely on the intended use and the user’s experience level. For beginners or those interested in light practice, a 1045 steel sword is a prudent choice due to its increased flexibility and resistance to breakage. Conversely, for advanced users or those participating in more rigorous cutting exercises, a 1060 steel sword is preferable for its superior hardness and edge retention. It is also important to consider factors such as weight, blade length, and balance, which can significantly affect the handling and performance of the sword. Consulting with experts and conducting thorough research will ensure that you choose a sword that aligns with your specific needs and preferences.