Everything You Need to Know about Fourdrinier Paper Machines: Their Paper Production Processes
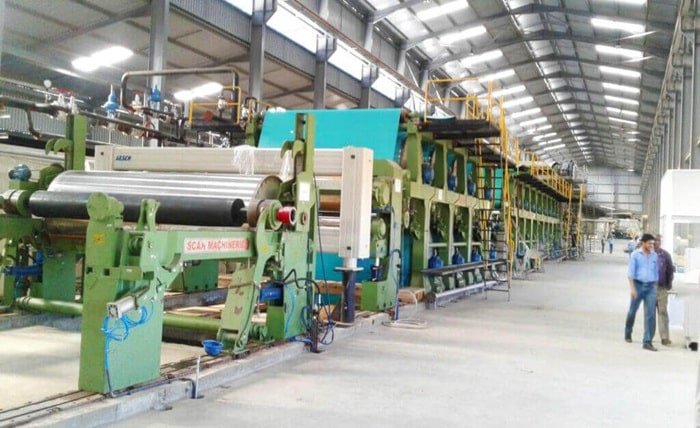
In the context of contemporary paper manufacturing, the Fourdrinier paper machine is one of its most essential features, as it efficiently converts raw materials into premium quality paper. The machine was named after its inventors, Henry and Sealy Fourdrinier, and it was created to enable the industry to transition from periodic production to continuous production in the early 19th century. During this time, these machines became an integral part of the paper production process due to their complex design and advanced technology. This guide will analyze the primary parts, mechanisms, functions, and benefits of these machines, as well as illustrate the role they perform in the creation of the paper products we interact with daily.
For more in-depth information you should view from Fourdrinier Paper Machine – UDTECH
What is a Fourdrinier paper machine and how does it function?
Learning the basic parts of a Fourdrinier machine
Each part of the Fourdrinier paper machine plays a distinct role throughout the manufacturing process, and all parts are essential. For this machine, the headbox is arguably the most important component as it generates a slurry of pulp and disburses it evenly over the moving wire or forming fabric. Initially, the wire section is an endless belt of fine mesh that serves to partially orient the fibers and drain the water. The almost complete sheet is then transported by press rolls and felt to the press section where moisture content is further reduced. Now, the paper is set onto drying cylinders and calendar rolls to ensure it is dried as well as smoothed for use.View Fourdrinier Paper Machine – UDTECH for More Details
The formation of paper on a fourdrinier machine
The process for paper formation on a Fourdrinier machine begins with the headbox evenly feeding the dilute pulp slurry of water and cellulose fibers onto a moving wire. As the wire moves, it passes over a drainage point and through suction, allowing water to drain through the fine mesh towards gravity, resulting in a mat of interwoven fibers. At this stage, the fibers align with the wire, which is motion that has a strong impact on the strength and texture of the paper. Next, the wet sheet is transported to the press section, which eliminates more of the moisture content and begins to set the structure for the drying and finishing processes that will occur later.
The design of the Fourdrinier machine has changed over time
The Fourdrinier machine has seen the introduction of many innovations over the years, enabling improvements in efficiency, quality of output, and sustainability in the operation. The automated control systems for the headbox consistencies, as well as fiber dispersion, have inline the products uniformity. Furthermore, advancements to vacuum technology and wire design have greatly improved the speed of the water extraction, which saves energy for the later stages of drying. To further these principles, new modern fourdrinier machines also make use of closed-looped water systems, reducing waste and increasing sustainability within the paper production process.
In what ways did the Fourdrinier machine mark a shift in the paper industry?
The consequential influence of continuously producing sheets when it comes to paper is due to the work of the Fourdrinier being the new milestone of innovation in the mechanization of paper. This change replaced the labor-intensive task of creating separate sheets of paper with one that was scalable and could be done with greater ease. The machine was able to pour fiber slurry onto a moving wire mesh and make it possible for sheets to be produced uniformly and consistently which made it easier for production to take place. With this, less time was needed to be spent on paper production and lower amounts of money was required due to the efficiency of labors skill sets.
The differences of Fourdrinier machines and fourdrinier machines versus Fourdrinier machine.
Even though the Fourdrinier machine and the cylinder machine are considered cornerstones of paper production, they have vast differences when it comes to design and functionality. A distinguishing feature of the Fourdrinier machine is that a moving wire mesh is used to make a paper web which can be produced at a much faster pace and for a wider selection of paper grades. Conversely, the cylinder machine makes use of rotating cylinders that can be used to form molds of individual sheets which is easier for multi-ply materials such as cardboard. Even with this ability, the adaptiveness and adn efficiency of the Fourdrinier machine are superior, thus being more beneficial for large scale production.
Improvements in the Grades and Quality of Papers
The Fourdrinier machine is an invention that has increased the quality and grade variety of papermaking. Modern improvements such as accuracy in water removal and advanced technologies in fiber distribution have made it possible to produce smooth, strong, and consistent papers. The ability to manufacture an increased variety of paper grades has also broadened in scope to serve various industries, from fine writing to packaging materials. This advancement in technology illustrates the continuous contribution of the Fourdrinier machine to the paper industry’s development.
What are the principle divisions of a Fourdrinier paper machine?
The role of the wire part of the paper machine
The wire part is one of the fundamental components of the Fourdrinier paper machine, where the basic web of paper is created. At this section, a mixture of water and fibers termed as pulp is spread evenly over the moving wire mesh termed as “wire”. At this stage, through the mesh, water is extracted from the pulp due to gravity and suction, and it results in a mat of fibers. To achieve uniform distribution of fibers, it is imperative that the tension and the speed of the wire be right. The accuracy and the efficiency of the wire section directly determine the quality, texture, and characteristics of the paper manufactured.
Comprehending the press segment and its functions
The press section, which comes after the wire section, is crucial in further reducing the water content of the paper web. This step is accomplished by forcing the uncomplete sheet through a succession of rotary press rolls that mechanically pump out more water. In addition to volume-to-surface density ratios, effective pressing increases mechanical properties of the paper and also smoothens the sheet and its surface. Efficient removal of water in this phase is important in subsequent drying processes, further reducing costs and saving the environment.
The drying process in Fourdrinier machines
The web drying process is the last step in the Fourdrinier paper machine. It consists of application of heat to the web so that remaining moisture can be evaporated. The web is carried over a set of steam-heated cylinders or drying drums. These should heat the web uniformly throughout its surface. Every step of the drying process is achieved with a constant speed and the temperature used is varied, otherwise defects will arise, such as curling or uneven shrinkage of the web. Apart from reducing the moisture content, drying also keeps the dimensions of the paper stable and reduces the wear on the paper during its subsequent machining.
Who developed the Fourdrinier machine, and during what period of time was it invented?
The Supporting Role of Henry and Sealy Fourdrinier
Henry and Sealy Fourdrinier, English siblings of a wealthy stationery business family, contributed significantly towards refining the technology used in the manufacture of paper. Their monetary assistance in furthering the research for the construction and refinement of continuous papermaking machines which later became known as the Fourdrinier machine was astounding. They finances the development of an early version of the machine and saw it transformed into something functional and financially profitable. Although the type of technology was astonishing, the Fourdrinier brothers had severe financial issues because of the development cost their business incurred and the lack of profit out of their spending. Still, their contributions serve as the basis of modern methods of producing papers.
John Gamble’s Patent And Bryan Donkin’s Section
An Englishman known as John Gamble was pivotal throughout the development phases of the Fourdrinier machine. In 1801, he patented an invention designed towards making the process of paper manufacturing easier by automating the mechanized steps of the labor intensive craft. Bryan Donkin, a skilled engineer, subsequently improved Gamble’s design, solving its mechanical problems and making it more efficient. At Frogmore Mill, Donkin built the first fully functional Fourdrinier machine in 1803, which is believed to have revolutionized the history of paper production. Thanks to his engineering skills, the machine was able to work and be used widely in the industry.
The Importance of Frogmore Mill In The History Of Paper Manufacturing Machines
Frogmore Mill in Hertfordshire, England, is famous for being the first and oldest operational site of the Fourdrinier machine in the world, where it was installed and put into operation in 1803. This achievement marked the beginning of extensive and continuous production of paper within industries due to its improved speed and reliability. Now, Frogmore Mill is visited worldwide as a historical site because of its importance in the advancement of technology in the global paper production industry.
What are the grades of paper produced on a Fourdrinier machine? Different types of paper produced on Fourdrinier The Fourdrinier machine produces different grades of paper for use in several fields and sectors. Some of them are news papers, printing and writing documents, tissue paper, and some special papers used for packaging and as decorative papers. Specific characteristics such as thickness, smoothness, opacity, etc. are achieved by manipulating important process variables like fiber type, additive materials, and machine settings. Controlled features of the paper, and versatile use of the machines makes them important ingredients for modern paper manufacture. The Fourdrinier machines make possible the manufacture of both standard and specially made products to meet market needs. Producing paperboard on Fourdrinier machines Paperboard, which is a relatively thicker and stiffer type of paper, can also be produced easily in Fourdrinier machines. The use of multilayer headboxes or other subsequent processes gives the machine the capability of producing paperboard of greater structural strength and rigidness. This makes it very useful as packaging material, folding cartons, and graphic board products. Different thickness and surface quality of paperboard produced by the machine are ensured by the Fourdrinier process in order to satisfy the demanding performance and appearance standards set by the end users.
How does the Fourdrinier machine work on a mixture of pulp and water?
Suction or Vacuum glass, or box, systems, or cups remove water below the wire mesh aiding towards suctioning the water. These boxes are mounted with pumps called suction rolls. The suction rolls help in getting rid of water and retain the pulps for fiber consolidation assisting in sheet formation. The suction helps in faster dewatering and enhances taking shape along the wire, improving quality and physical characteristics of the paper.
Regulating pulp consistency in accordance with paper quality requirements
For the uniformity of paper characteristics, the pulp consistency must be maintained at an optimum level during the Fourdrinier process. Consistency is defined as the amount of fiber present in the pulp slurry compared to water, and it can be managed by means of mechanical dilution systems working in conjunction with constant supervision. If the consistency levels are lower than the desired result, the fibers will not bond properly, resulting in weaker paper. However, if the consistency is high, there may be problems with the paper sheet such as non-homogeneity or defects. Careful monitoring of the consistency allows fibers to be evenly distributed across the screen wire, thus enhancing the quality, strength, and smoothness of the surface of the product.
What are the newest advancements in the Fourdrinier machine technology?
The Benefits and Uses of Twin Wire Fourdrinier Machines
Twin wire Fourdrinier machines mark a major milestone in the papermaking technology as they enhance the dewatering process and have better formation properties. These machines have a pair of parallel forming wires that compress the pulp from both sides, which allows for more uniform fiber orientation and better water removal than single wire systems. As a consequence, the paper is stronger, production speeds increase, and the amount of energy needed to dry the paper is reduced. Twin wire systems have a greater advantage when producing high quality grades of paper and board, especially light specialty papers and packaging materials that are used for blinding, where uniformity and mechanical properties are essential.
Refinements in machine-dimension control for MD and CD in Fourdrinier machines have resulted to the significant development of quality in paper manufacturing. Sophisticated control automation now utilizes modern sensors and actuators that measure and control basis weight, moisture content, fiber orientation, and other parameters as they happen. Improvement in MD and CD control guarantees a constant paper sheet thickness with a uniform strength distribution. These technological advancements provide a solution to the production variabilities which minimize waste and yield a finished product expected to be of high standards, suitable for precision engineering works.
Advancing the smoothness and other surface properties of the paper has also widened the range of paper products produced. The introduction of a higher grade paper with more superior surface characteristics has brought innovation in the preparation of paperware texture and smoothness. These includes advanced coatings, press section design, and calendaring systems. For example, modern calendaring systems apply precision rollers to the paper surface to optimize it for printing, packaging, or specialty purposes. Moreover, advancements in surface sizing and coating systems have better specify the ink holdout, reduced absorption variability, and increased printability satisfying the needs of the high-quality printing and packaging.