The Role of Welding in the Industrial Sector: A Review of Its Impact on Productivity
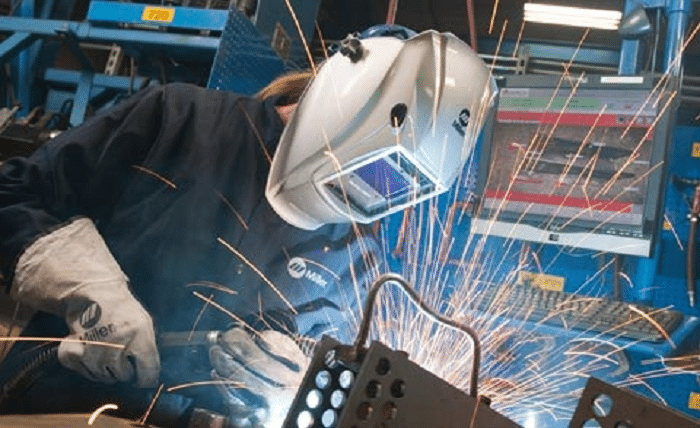
Introduction:
Welding in the industrial sectors is not only about sparks and metal. It is the ubiquitous but unseen glue behind our physical infrastructure, transportation systems, energy generation and thousands of manufactured products. The benefits of welding are even more essential in today’s high-speed economy, where productivity gains can turn the tide.
Note: Explore our high-end welding wire products ผลิตภัณฑ์ลวดเชื่อม at: https://www.udo.co.th/category_product/กลุ่มลวดเชื่อม/. Professional Or Hobbyist, We have The Wire You Need. Read more details on our product information and have a discussion with our expert team. Upgrade your welding projects with high-grade wires and professional guidance. Follow the link above and find out more here.
This means we can review the importance of welding for the modern industry and how wrong operations in it can take a toll on productivity.What is so Important in Industry to Welding?Welding is not one process; it is a diverse family of processes each having their own strengths. The broad applicability of welding makes it a highly valuable skill in many industries, including:
Building and fabrication: Our buildings, including the massive bridges that span rivers and bays, rely on welding to provide the structural integrity that makes them safe.You cannot look around and not see the remnants of welding in just about every manufactured items you physically interact with on a daily basis, from cars and household appliances to your electronic gadgets and some medical devices.
Energy: Pipelines, power plants, and renewable energy systems all use welding to move energy safely and keep it contained.Welding provides the strength and precision necessary for ships, airplanes, trains, and automobiles to exist, and without welding, transportation would likely be non-existent.
What Visual-Quality Drivers In Welding:
Automation and Robotics: The automation of welding in a big way has transformed the productivity since robotic welding systems have been introduced. Robots can weld faster with fewer mistakes and less rework than humans.
Welding Engineer: Welding technology is no longer just used for connecting different types of steels; processes have evolved to be able to join a variety of materials, from high-strength alloys and composites to plastics. This in turn allows to manufacturer lighter, stronger and better performing products.
Quality control technologies – non-destructive testing (NDT) methods, such as X-ray and ultrasonic inspection allows to verify quality and structural integrity of welds reducing risk of failure and downtime.
A skilled workforce: The welding industry is suffering a shortage of certified welders which make their skills even more valuable. Training and apprenticeships are the key to keep well-trained workforce.
Effects of welding on productivityThe effects of welding on productivity are as follows :
The productivity effect of welding is out and out recognisable. This is what this translates to in the real world:Automated welding systems and efficient processes cut production cycles, getting manufacturers quickly back on line to meet tight deadlines and respond promptly to market demand.Now makers can experience a substantial cost savings throughout manufacturing as a result of less error, product waste and downtime.Heightened Product Quality: Uniform, high-quality welds mean items are better made and much more reliable, thereby increasing customer satisfaction and encouraging brand loyalty.Progress:New welding technics make new construction possibilities possible that were impossible only 10 years ago.
Challenges and Opportunities:
Welding, as a productivity powerhouse, has its constraints in the current state of the industry. This scarcity and the ongoing technical developments means that investment and innovation is required.Yet there are new potentials on the block. Welding processes have enabled 3D printing of parts, additively manufacturing (AM), promising the ability to revolutionize manufacturing by producing parts on-demand that are often impossibly complex. The increasing push toward environmentally friendlier manufacturing practices makes developing sustainable welding methods a natural fit.
Conclusion:
The welding done in the industry is an invisible hero involved in this new modern age of manufacturing. The effect it has on productivity is far-reaching, influencing innovation, cost reduction and the delivery of products with consistent high-quality across an array of industries. As technologies develop further welding will continue to make the world more productive and provide bright future with confidence for industries across the globe. By creating initiatives to retain welders, adopting automation and continuing the technological evolution of welding, businesses have the potential to fully utilize welding capabilities to reach new heights in work efficiency and innovation.