FRP Grating: The Durable, Non-Slip Solution for Harsh Environments
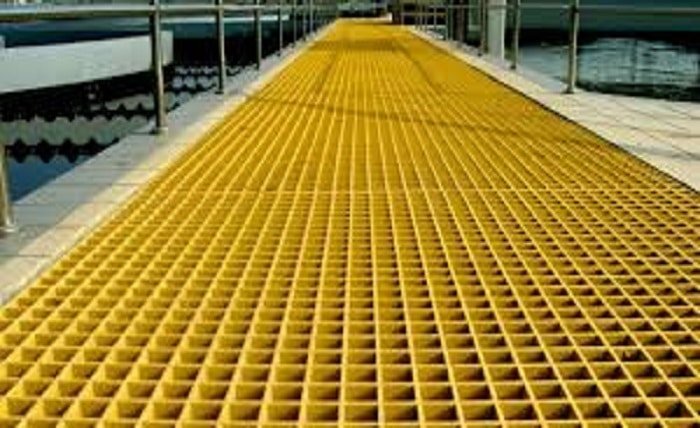
Introduction
For industries requiring a durable, low-maintenance solution to withstand the demands of harsh environments, FRP grating has become the go-to choice. This advanced material, made from Fiber Reinforced Polymer, offers unmatched resistance to corrosion, a non-slip surface for enhanced safety, and strength to handle heavy loads. In settings like oil and gas, water treatment, and chemical processing, FRP grating is proving its value as a versatile and reliable option. Here’s why FRP grating outperforms traditional grating materials and what makes it the top choice for demanding industrial applications.
What is FRP Grating and How Does it Work?
The Composition and Strength of FRP Grating
FRP grating is composed of high-strength fibers embedded in a polymer matrix, resulting in a material that’s exceptionally durable, corrosion-resistant, and lightweight. This unique composition makes FRP ideal for settings exposed to moisture, chemicals, or saltwater, where traditional grating materials would require frequent upkeep. Unlike metals, FRP grating maintains its structural integrity without rusting or degrading, even in the toughest conditions. These properties make it a smart choice for industrial environments where reliable performance is key.
FRP Grating vs. Traditional Grating Options
When comparing FRP grating to materials like steel, aluminum, or wood, the advantages of FRP are clear. Steel grating, while strong, is prone to rust and requires regular maintenance, especially in high-moisture or corrosive environments. Aluminum, though lightweight, lacks the durability needed for many industrial applications, and wood degrades rapidly without chemical treatment. FRP grating combines the best of both worlds: it’s lightweight for easy installation but also strong enough to support high loads. For those seeking a low-maintenance, corrosion-resistant option, FRP grating is a superior alternative. For further insights, check out these advantages of FRP grating.
Key Benefits of FRP Grating for Harsh Environments
Non-Slip Surface for Enhanced Safety
FRP grating’s non-slip surface offers a crucial safety advantage in industrial settings where wet, oily, or otherwise hazardous conditions are common. Its surface design minimizes slip risks, helping prevent accidents on walkways, platforms, and stairways. This is particularly important in high-traffic areas and for projects where safety compliance is essential. By providing a stable, slip-resistant footing, FRP grating significantly reduces the likelihood of slips and falls, making it a wise choice for industries prioritizing worker safety.
Corrosion Resistance and Long-Term Durability
One of the primary reasons industries turn to FRP grating is its ability to resist corrosion over long periods, even in extreme environments. Whether exposed to saltwater, harsh chemicals, or regular humidity, FRP grating maintains its strength and integrity without the need for constant maintenance. This durability leads to fewer replacements and lower maintenance costs, making it a cost-effective solution in the long run. Companies in sectors like wastewater treatment, oil and gas, and chemical processing benefit greatly from FRP’s resistance to corrosive elements, as it reduces costly downtime associated with repairs and replacements.
Applications of FRP Grating in Harsh Industrial Environments
Key Industries and Uses of FRP Grating
FRP grating is widely adopted in industries with challenging conditions, such as oil and gas, water treatment, chemical processing, and food manufacturing. Each of these sectors benefits from the specific qualities of FRP. For example, in oil and gas facilities, FRP grating provides a slip-resistant, corrosion-proof surface ideal for walkways and platforms. Water treatment facilities rely on FRP grating for its resistance to both moisture and chemicals, ensuring long-lasting safety and stability in wet environments. Chemical plants utilize FRP grating due to its non-corrosive properties, which help protect against harsh chemicals while keeping workers safe on a slip-resistant surface.
Case Studies and Examples of FRP Grating in Action
Several projects in Australia highlight FRP grating’s success in real-world industrial settings. For instance, a water treatment plant in Queensland installed FRP grating along elevated platforms and walkways, reporting significant reductions in maintenance and replacement needs. The grating’s ability to withstand continuous chemical exposure and maintain a non-slip surface was essential for operational safety and efficiency. Similarly, an oil refinery in Western Australia used FRP grating to improve safety in high-traffic areas that previously experienced rapid deterioration with other materials. These examples underscore how FRP grating provides a long-lasting, low-maintenance solution in harsh, high-exposure environments.
The Future of FRP Grating in Industrial Safety and Sustainability
Eco-Friendly Benefits of FRP Grating
As industries move toward more sustainable practices, FRP grating stands out for its eco-friendly profile. Its extended lifespan reduces the need for frequent replacements, thereby minimizing material waste. Additionally, FRP grating does not require chemical treatments or coatings, and it doesn’t release harmful substances into the environment. This makes FRP an ideal choice for companies looking to balance performance with sustainability, aligning with industrial goals to reduce environmental impact without sacrificing quality or safety.
Meeting the Demand for Safer, Resilient Industrial Materials
In Australia and beyond, the demand for safer, more resilient industrial materials continues to grow. FRP grating meets this demand with its non-slip, non-conductive surface, which provides additional safety in settings where electrical hazards or slippery conditions are concerns. For companies aiming to enhance worker safety and comply with evolving safety standards, FRP grating is an effective solution. Its durability and resistance to challenging environmental factors ensure that FRP remains a viable choice as industries advance.
Conclusion
FRP grating has proven itself as a top-tier solution for harsh environments, combining strength, corrosion resistance, and slip-resistant properties that make it ideal for industrial applications. From oil refineries to water treatment facilities, FRP grating offers an adaptable, long-lasting alternative to traditional materials, supporting safer, more efficient operations. As industrial safety and sustainability demands rise, FRP grating’s role in creating resilient infrastructure will only grow. For industries looking to invest in durable, low-maintenance grating solutions, FRP is the forward-thinking choice that meets the challenges of today and tomorrow.
Frequently Asked Questions (FAQs)
Q1: What makes FRP grating slip-resistant? A1: FRP grating features a textured surface that enhances grip and minimizes the risk of slips, even in wet or oily conditions. This slip-resistant quality makes it an excellent choice for high-traffic industrial areas where safety is a priority.
Q2: How does FRP grating compare to steel in terms of maintenance? A2: Unlike steel, which can corrode and requires regular upkeep, FRP grating is highly resistant to corrosion and requires minimal maintenance. This results in significant cost savings over its lifespan, especially in high-moisture or chemical-prone environments.
Q3: Is FRP grating suitable for exposure to chemicals? A3: Yes, FRP grating is designed to withstand exposure to a variety of chemicals, making it ideal for use in chemical plants, wastewater treatment facilities, and other industries where chemical resistance is essential.
Q4: How does FRP grating support sustainability? A4: FRP grating is sustainable due to its long lifespan and low replacement needs, which reduce material waste. Additionally, it doesn’t require chemical treatments, making it an environmentally friendly choice for industries aiming to reduce their ecological footprint.